Plasma Nitriding – Technical Information
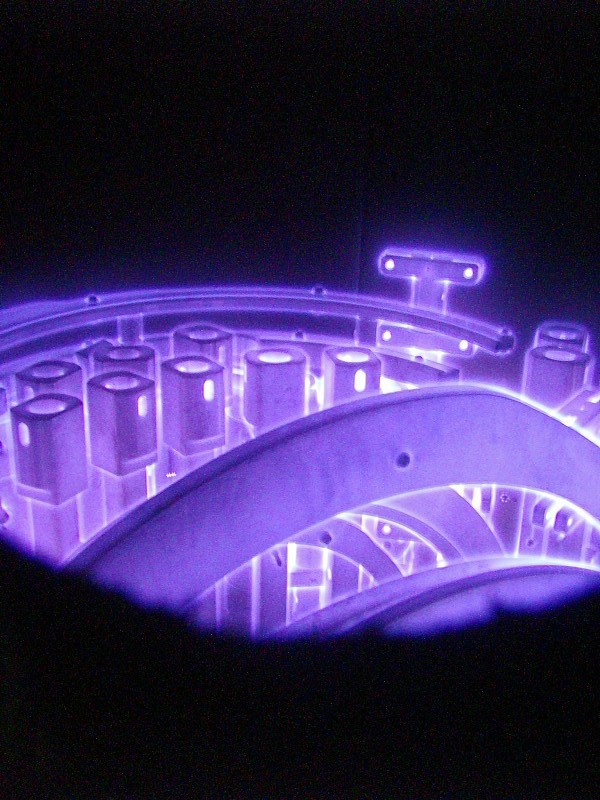
Plasma (Ion) Nitriding
Plasma nitriding is a surface hardening process which is apllied ferrous materials.
Plasma Nitriding process which is performed in special designed vacuum furnaces, is achieved by directing the ionized process gases by electric current to the workpieces.
When the workpieces are reached to diffusion temperature by slow heating up, by means of the plasma phase surrounding the workpieces uniformly, nitrogen atoms start to diffuse into from the surface
The plasma nitriding process temperature can be between 350-580 ° C, depending on the type of material, the heat treatments previously applied, and the desired surface properties. The process time can range from 15 minutes to 120 hours depending on the desired characteristics.
Proporties
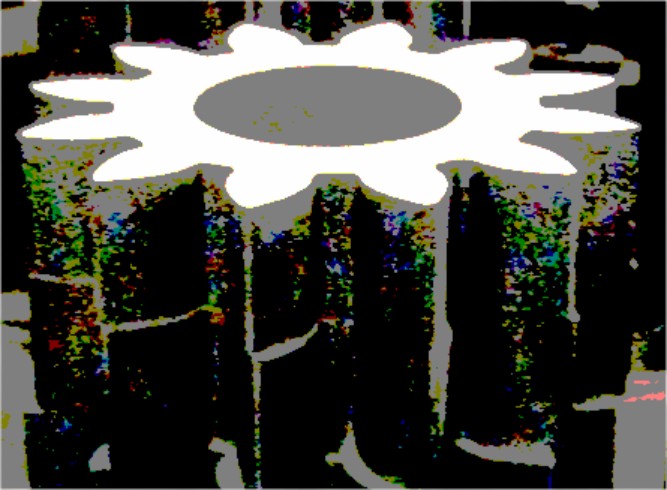
- Plasma Nitriding,
- Gears
- Cams
- Shafts
- Machine Parts
- Plastic Moulds
- Metal Injection Dies
- Hot Forging Dies
- Hydraulic Cylinders
As a summary,
It offers significant advantages in all kinds of industrial applications with friction and wear.
Advantages of Plasma Nitriding
- Increases wear resistance,
- Extends fatigue life,
- Minimizes distortion and dimensional changes,
- Provides high surface hardness,
- Provides high dimensional loyalty,
- White layer control capability is very high.
- Improves corrosion resistance in unalloyed and low alloyed steels,,
- After nitriding, clean and bright surfaces are obtained,
- It does not pollute environment, it does not harm human health.
- More uniform hardness distribution
- Ability to adjust the hardness profile
- Closing the sections with mechanical masking of the section where will not ne hardened
- Minimizing capability of hardness decreasing problems at low temperatures
By means of these advantages of Plasma Nitriding;
- Automotive and automotive suppliers industry
- Machinery manufacturing industry
- Machinery spare parts industry
- Heavy industrial machines
- Hydraulic work machines
- Die industry
are applicable in a wide range applications.