Advantages of Plasma Nitriding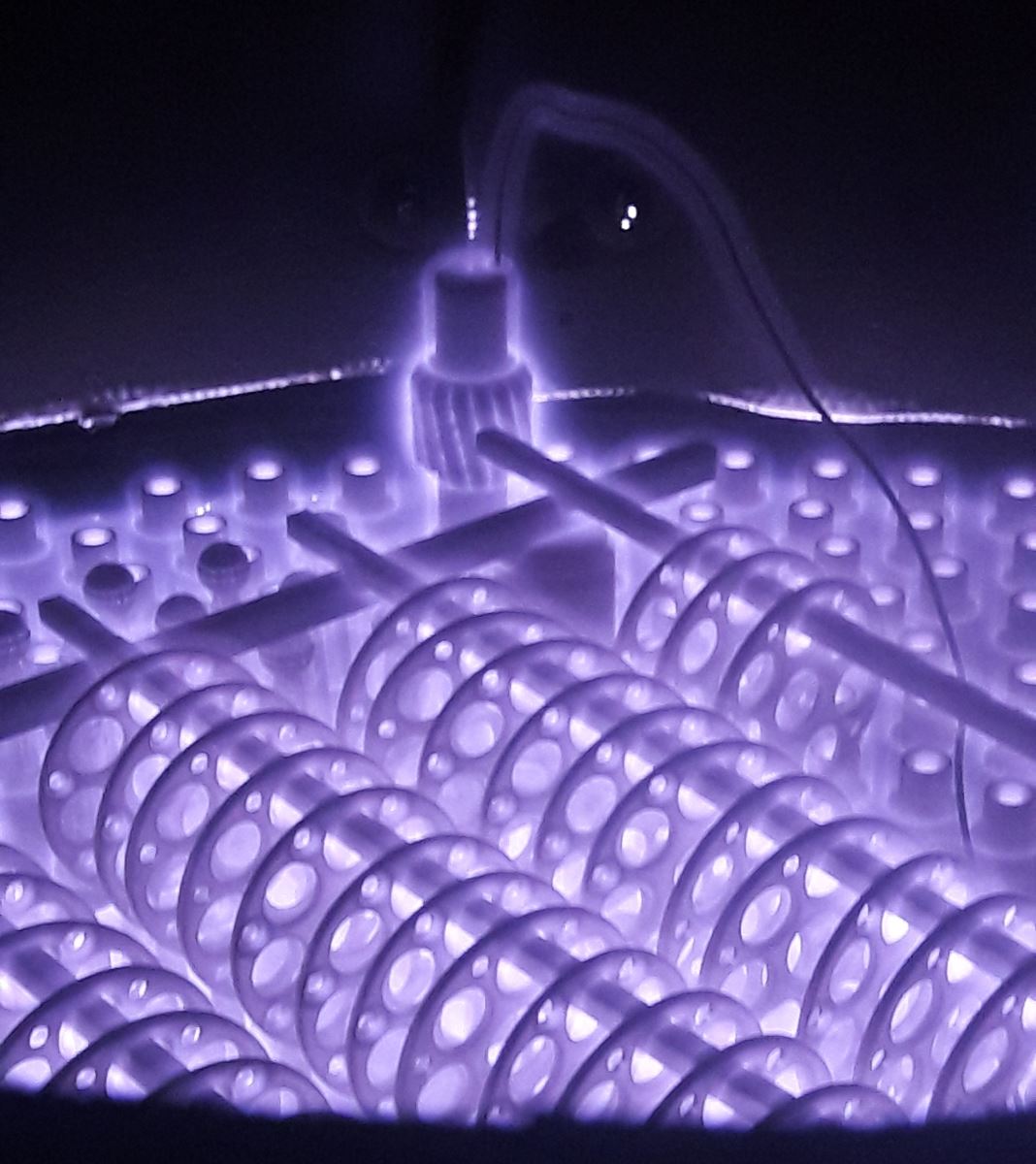
Nitriding process is used for increasing of surface hardness and wear resistance of steel and cast iron materials differs from other heat treatment processes because there is not any phase change (it is done at ferritic phase) during the process. Plasma nitriding has significant advantages because of that it has lowest process temperature. Plasma Nitriding minimizes dimensional changes and distortions and has a wide range capability for nitriding of austenized cold-work tool steels and high speed steels. During the process, use of the process gases and flexible adjustment capability of gas percentages is a significant metallurgical advantage.
Plasma Nitriding process has the following advantages when compared with other nitriding processes:
- Applicable for all steel and forging materials, and also for Ti.
- Possible to do nitriding at lower temperatures beginning from 350°C.
- Minimizes distortion and dimensional changes on the part.
- High control capability of surface treatment.
- Increases fatique resistance.
- High capability of white layer control
- Increases corrosion resistance of low alloy and carbon steels.
- Clean and bright surfaces after nitriding process.
- Uniform hardness distribution than other nitriding processes.
- Possible to adjust optimum hardness-depth value.
- Possible to protect surfaces compeletely which will not be nitrided by mechanical masking.
- No harmful effect on human and environment.
- Reproducible results, suitable for automation.
- Depending on the required nitriding case depth, nitriding process can be applicable
with the durations starting from a few minutes to 10 days.
- Applicable for the parts has a weight starting from grams to a few tons.